Making your supply chain more effective and sustainable with technology
INQOVA attended the Kingpins Show in Amsterdam to explore how technology can reduce costs and fabric waste by improving communication between denim mills and customers.
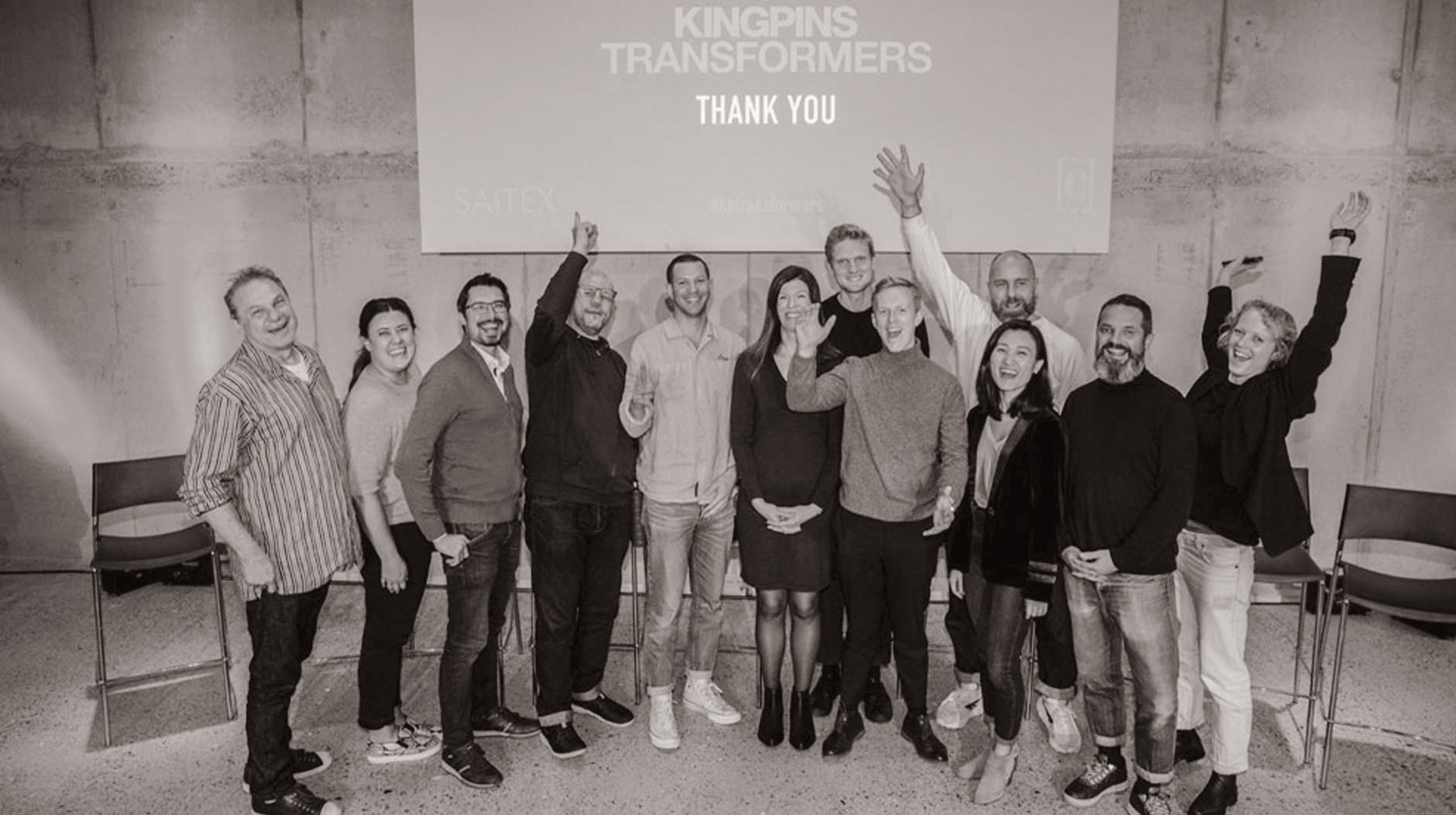
Before beginning to optimise the communication between the process of merchandising, purchasing and requesting samples, we first have to understand the challenges denim mills currently face in the supply chain.
During the B2B process of a fabric mill, 70-80% of the supply chain effectiveness is lost along the way due to poor communication, where stakeholders are not getting the right information when and where they need it. Most mills have the product data available, but a lot of the customer data is not captured and organised in a digestible way, resulting in miscommunication along the way.
You may have even experienced this ineffective communication model first-hand at trade show events. Typically, buyers will meet the mills at booths, request samples and note down the contact details on a piece of paper. Some time passes, and the shipment of 50-100 samples arrives in a box. At that point, you might have already forgotten the reason for requesting the samples in the first place. The current process of requesting samples can be timely, costly, and most importantly, wasteful.
So, what’s the solution? Technology, technology, technology.
With the rights tools to capture and process data, we can achieve a data-driven understanding of the relationship between customer and product. This way, mills can service customers better by predicting patterns to offer better products and advice on what is in demand by the market.
An example could be creating a digital 3D model, as well as a mobile app. This way we can support staff and customers in the sales and sample ordering process. The app can scan the QR code on the fabric to retrieve all the information you need, keep records of your selections, and get personalised recommendations. With this approach, we can help mills with product development over time, and reduce the need for physical samples being made and shipped around the world.
Even though Denim is a more difficult fabric to digitise - as the laundry process can make the texture irregular - the potential of 3D denim is truly limitless. At INQOVA, we have tested this out by building a 3D scanning studio in Hong Kong to create a digital 3D version of an existing physical garment. Not only can it be replicated and distributed into infinity with no marginal cost, but it can also be animated to simulate human movement.